Moventas confía en el análisis del ruido de Barkhausen.
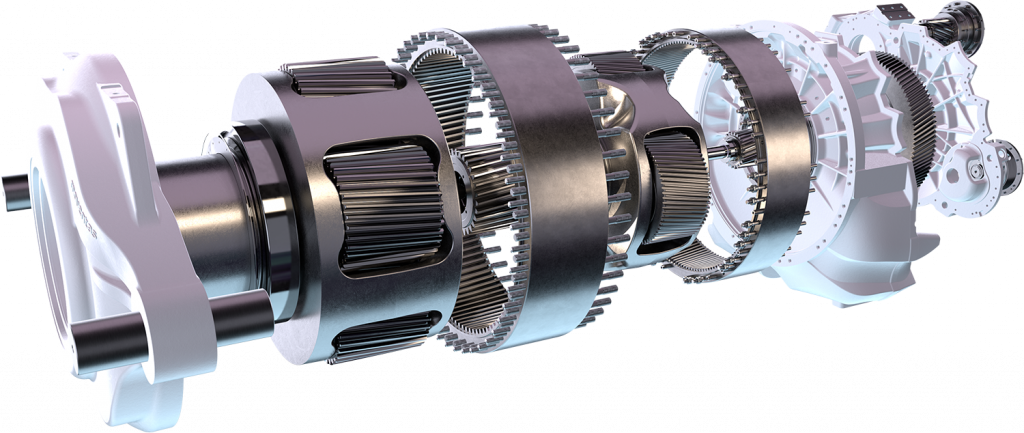
Moventas (adquirida por Flender), experta en la fabricación de multiplicadoras para aerogeneradores, lleva 40 años en el sector y le apasiona innovar en soluciones para multiplicadoras que permitan ahorrar costes y funcionar sin problemas. Durante los últimos 30 años, desde el primer sistema Barkhausen hasta el último sistema robotizado, Moventas ha confiado su inspección de rectificado a Stresstech y a sus sistemas de medición de ruido Barkhausen.
Requisitos de alta calidad
Como componente clave de los aerogeneradores, las cajas de engranajes deben cumplir unos requisitos extremadamente exigentes, ya que las grandes cajas de engranajes están sometidas a cargas extremas, como los cambios de velocidad del viento. La sustitución de una multiplicadora es una de las operaciones de mantenimiento más caras que requieren los aerogeneradores, por lo que la calidad de los componentes de la multiplicadora debe ser impecable.
En Moventas, la garantía de calidad forma parte integrante de las operaciones diarias y del liderazgo de la empresa. Todos los procesos clave de fabricación se realizan internamente, y son bien conocidos y solicitados por su diseño y fabricación de alta calidad.
Hoy en día, los fabricantes de aerogeneradores exigen que las superficies se sometan a pruebas para detectar la posibilidad de quemaduras por rectificado. Las quemaduras por rectificado son daños térmicos que se producen en la superficie durante los procesos de rectificado. Las quemaduras por rectificado provocan decoloraciones locales en la superficie, pueden ablandar o endurecer las capas superficiales y causar tensiones residuales no deseadas.
Taisto Kymäläinen, responsable de calidad de Moventas, recuerda que a mediados de los años 90 se desarrollaron máquinas rectificadoras en las que la velocidad de rectificado aumentaba drásticamente, pero con el desarrollo de nuevas máquinas era posible utilizar una mayor velocidad de avance, lo que incrementaba el riesgo de quemaduras por rectificado.
Detección de quemaduras por rectificado y optimización de procesos
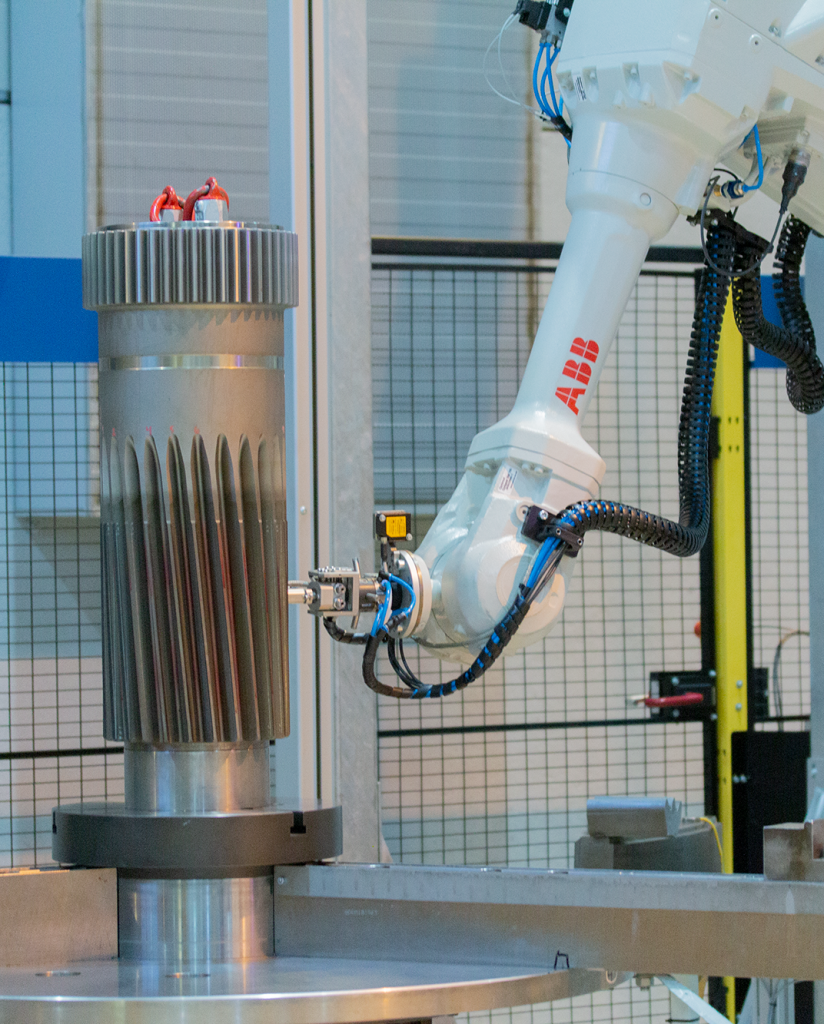
Otto Lähdekorpi, ingeniero de calidad de Moventas, explica que Moventas realiza un análisis de ruido Barkhausen en todas las superficies rectificadas con sus engranajes y ejes. Las mediciones se realizan en componentes de nueva fabricación, así como en componentes rectificados con fines de reacondicionamiento.
Moventas es un usuario avanzado del análisis de ruido Barkhausen y lo utiliza más allá de la mera clasificación de las muestras buenas entre las quemadas. Taisto Kymäläinen explica que el método de Barkhausen permite la detección precoz de daños, ya que el análisis de ruido de Barkhausen reacciona ante los cambios más pequeños en una microestructura, por lo que puede utilizarse para optimizar un proceso de rectificado y encontrar los parámetros de rectificado correctos. Por ejemplo, el análisis de ruido de Barkhausen puede revelar fallos en el refrigeramiento o el desgaste de la muela antes de que aparezca la quemadura real.
Dado que el análisis del ruido de Barkhausen es un método comparativo, los usuarios deben determinar los niveles aceptables para sus productos con el procedimiento de la muestra patrón. El procedimiento de la muestra patrón puede validarse, por ejemplo, con mediciones de difracción de rayos X o ataque nital. Cuando se establece el procedimiento de la muestra patrón, el análisis de ruido de Barkhausen es un método preciso para detectar cambios en la microestructura.
Por ejemplo, en Moventas han establecido una aceptación a cierto nivel de mp (parámetro magnetoelástico: tensión RMS del ruido Barkhausen medido), cuando el nivel de mp es un 20% superior, ya se puede ver la quemadura a simple vista. Moventas utilizó el ataque nital en su proceso para determinar los niveles de mp aceptables, sin embargo, el ruido Barkhausen reacciona a la quemadura por rectificado un 10-20% antes de que pueda verse con el ataque nital.
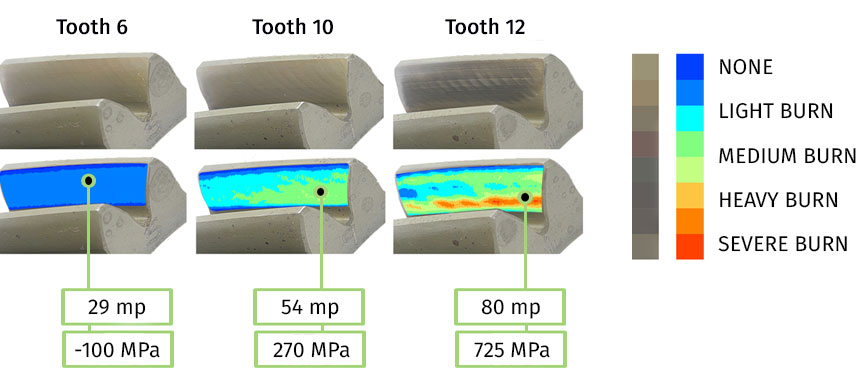
Los sensores de ruido Barkhausen requieren procedimientos de «masterización» regulares; el RoboScan ha facilitado esta tarea, ya que las muestras patrón se miden en cientos de programas con los mismos resultados. Si es necesario ajustar los sensores, el Roboscan permite ejecutar el sensor en el punto correcto y realizar los ajustes sin temor a que se produzcan cambios en los contactos.
Detección de quemaduras por rectificado y optimización de procesos
Taisto Kymäläinen explica que, a lo largo de los años, los tamaños de los engranajes han aumentado hasta 600 mm de altura del diente y que la medición manual del ruido Barkhausen resultaba improductiva y poco ergonómica. Un sistema robotizado de ruido Barkhausen resolvió ese problema, y ahora Moventas utiliza tres RoboScan de tamaño XL para realizar las mediciones de ruido Barkhausen.
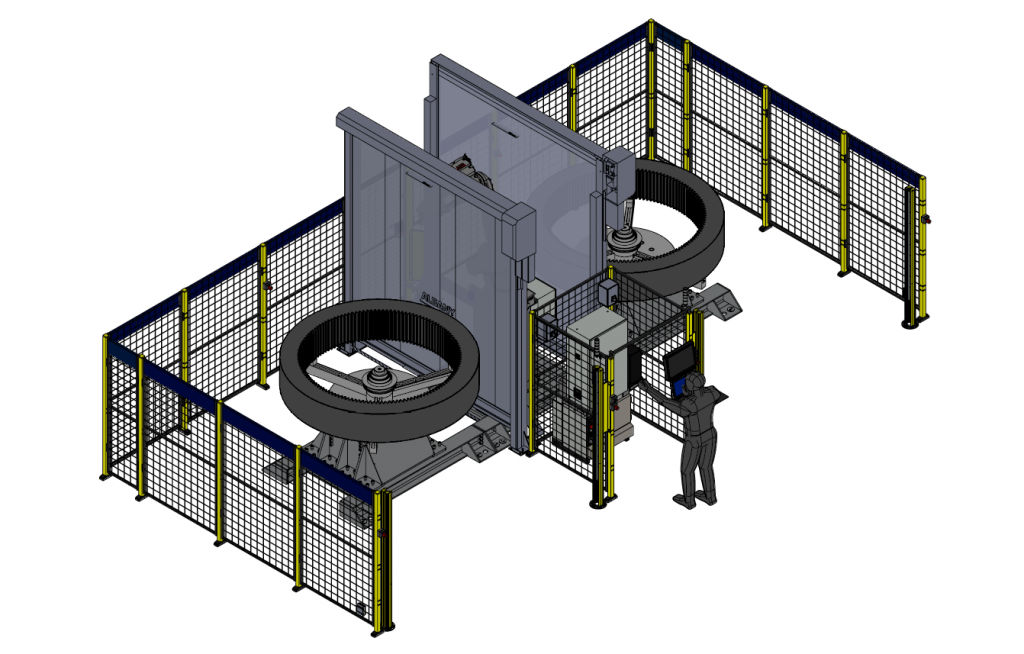
Con RoboScans, el operario no tiene que ser un experto en ruido de Barkhausen, ya que el sistema se encarga de todo y las mediciones son más rápidas y precisas. Otto Lähdekorpi recuerda que medir un engranaje de 180 dientes suele llevar unas dos horas, pero que con el sistema de medición manual previo se habría tardado el doble.
Las características y mejoras aportadas por los sistemas de medición de ruido de Barkhausen de Stresstech permiten garantizar la más alta precisión en las mediciones, lo que permite a Moventas seguir suministrando componentes de la mejor calidad a los clientes.
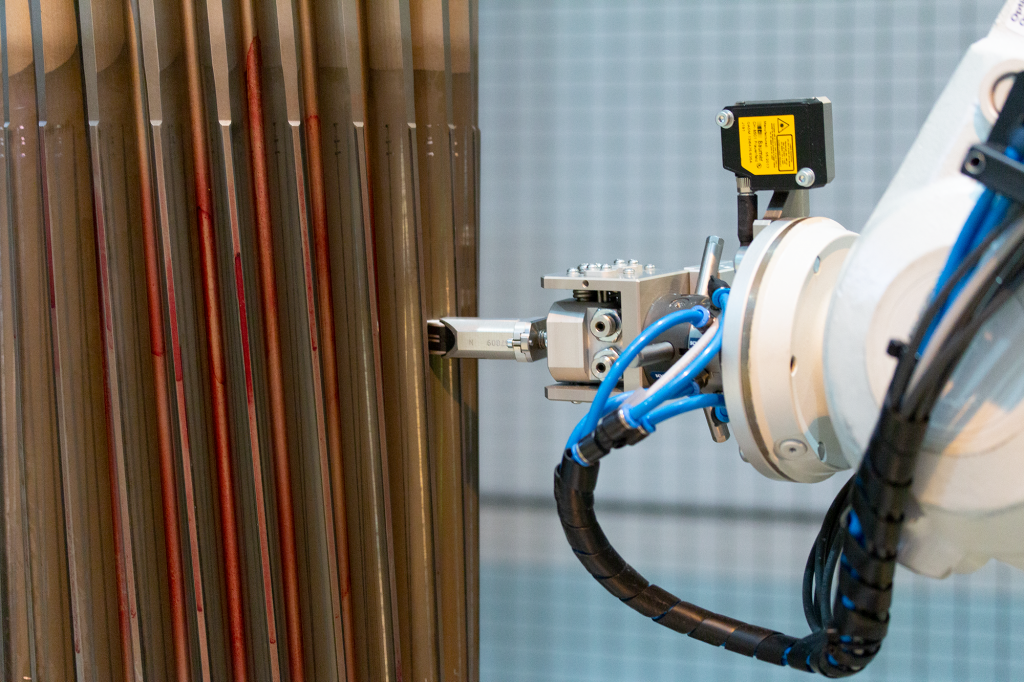
¿Necesita detectar quemaduras de rectificado?
¡Podemos ayudarle!
Nuestros ingenieros tienen décadas de experiencia ayudando a los clientes a encontrar el instrumento adecuado para su aplicación.